Global Chip Shortage - Why are we in this Crisis?
Date: February 24, 2022
What is the chip shortage?
The global chip shortage of 2020 - 2022 is an on-going problem affecting many industries and businesses. Those affected may not even be in manufacturing, but could be anyone who relies on modern technological devices.
Certain products are getting harder to source and/or the price of such goods is rising[1]. This has been felt severely in the automotive industry, with examples such as Nissan making half a million fewer vehicles[2]. The computer gaming industry has been similarly affected with gaming consoles such as XBox and Playstation, and PC graphics cards having long waiting lists and premium prices[3]. Hidden behind these shortages and price increases is an underlying problem - the inability of the supply of integrated circuits, also known as chips, to keep up with demand.
Where do chips come from?
Integrated circuits (ICs or simply chips) are in almost every product we use today. They are in our fridges, microwave ovens, washing machines, cars, headphones, TVs, phones, watches, toys, eftpos machines, lab equipment, air conditioning, and so many more devices.
Chips are cheap to make en-masse, but setting up the facilities to make them can take several years and billions of dollars. There is a limited number of these facilities, known as fabrication-plants or ‘fabs’, around the world[6].
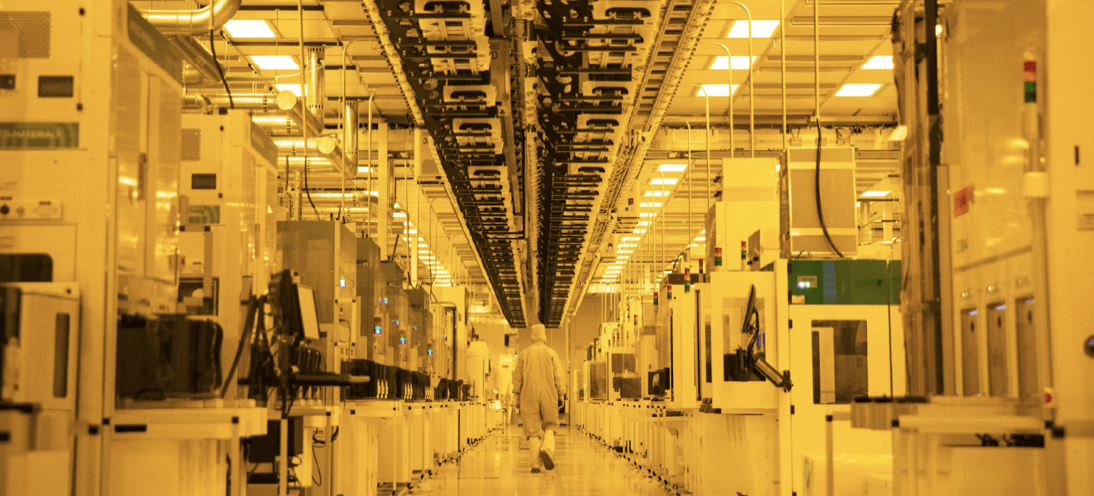
A lot of manufacturing of electronic goods (as well as non-electronic goods) were, or still are, produced by a production model of lean manufacturing, also known as just-in-time(JIT) manufacturing. JIT boils down to ordering components of a product just as they are needed to produce the item. This reduces waste from stock-piling components and the costs of storing these; it does however require a robust supply chain[7].
So, what happened before, during and after 2020 to cause the global chip shortage?
A perfect storm of problems coincided in a short enough time-frame to cause a singular problem which we now label as “The global chip shortage”.
- Geopolitical tensions were rising between the United States and China.
- Severe weather events at key fabrication-plants and serious fires at others, caused major production issues.
- The global pandemic which we will refer to as Covid-19 for the purposes of this article, which increased demand almost over night.
- Shipping and local deliveries slowing down the supply chain from raw material to finished product, which has also played a role in this shortage.
Let’s look at these four points in detail:
1. Trade Wars
The precursor to the Global Chip Shortage was the rise in tensions between the United States and China.
Then U.S. President Donald Trump initiated a trade-war with China as far back as 2018, which included a 25% tariff on Chinese imports, including semiconductors (IC chips) and their raw materials[15]. Now only 5% of chip imports to the U.S. are from China, but imports from other countries have not increased enough to offset the supply loss.
In another move in the trade war, in 2019, the same presidency banned the sale of U.S. semiconductors to the Chinese company Huawei. This caused some U.S. manufacturers to scale back production as their primary client was suddenly shut to them. China boosted production and began hoarding the stock. This further disrupted supply chains causing a long-term flow on effect, which is still being felt.
The Biden White House has not yet repealed the Trump tariffs. They have made negotiations with other countries to boost trade of semiconductor commodities, as well as measures to drastically increase American production capability.
In conjunction with this, a Japan - Korea trade war in 2019 started with Japan placing restrictions on raw materials that were used to create chips. Korean manufacturers such as SK Hynix and Samsung were impacted, which added to the destabilisation of the global supply chain.
2. Disasters
Taiwan drought
Taiwan, home to TSMC (Taiwan Semiconductor Manufacturing Company Ltd), which is one of the largest chip fab’s in the world, suffered a drought over the entire year of 2020. Taiwan usually relies on seasonal wet seasons to refill it’s reservoirs of water, but they did not get a reprieve until May of 2021 [10].
TSMC uses 156 million litres of purified water per day[9]. Much of this is recycled, and the company did not report any downturn in normal production levels. However it did prevent them from scaling up production to cope with the new heightened demand.
Texas Snowstorm
In February of 2021, the state of Texas suffered extreme cold weather for an unprecedented long time. Texas is home to many of the United States chip fabs, such as Samsung, Texas Instruments, NXP, Infineon, and others.
The cold weather and snow caused power-grid problems as well as staffing safety issues. Plants either shut their doors (on short notice) or went into emergency operating mode [13].
Fires
Nittobo suffered a factory fire in Fukishima, Japan in 2020. They are the world leaders in printed circuit board (PCB) substrate material[15]. This caused supply issues downstream in manufacturing for 6 months.
A large three-day fire raged through a Asahi Kasei Microsystems (AKM) factory in Japan in Oct of 2020. This high-end audio chip manufacturer disaster caused major supply problems for other audio manufacturers such as Solid State Logic, TASCAM, miniDSP, Merging Technologies, SPL of Germany, RME, and others [16].
A fire at a Renesas Japan (chip) fabrication plant, in March of 2021, caused a significant drop in capacity from that company. Production was fully restored by the end of that June [11].
As recently as 2nd of January 2022, a fire at a plant in Berlin, Germany, owned by ASML Holding has a lot of people worried. This plant manufactured the lithography machines which are sold to chip fabs. They are the largest supplier of these machines, and the only source for extreme ultraviolet (EUV) lithography machines [12].
3. The Pandemic
In late 2019, the Virus SARS-COV2 began causing the disease known as Covid-19, and reached pandemic status in early 2020. A lot of the global population was encouraged to stay at home to prevent further spread of the virus.This drove demand for work-at-home products such as laptops, webcams, new phones, etc, sky-high.
Also in hot-demand were entertainment devices such as PC graphics cards and gaming consoles. The PC graphics cards were also being competed for by crypto-miners causing even more demand [18]. Some chip fab’s changed their tooling to accommodate more for the consumer market to meet this demand, which then impacted the automotive industry again [17].
An unprecedented rise in e-commerce happened almost over night as public spaces were closed due to the pandemic. This put a strain on shipping and last-mile delivery, not to mention port-workers and truckers either staying home or getting sick.
4. Shipping and Supply Chain
The global supply chain of everything, including products involved in chip making, is primarily made up of shipping and ports. Ships account for 80% of global trade. The system is a complex industry of logistics, and pre-pandemic running at near capacity for efficiency.
When demand for trade goods did not slacken after the Christmas peak of 2019, strain was put on the system. Then the pandemic became global, causing shipping and dock workers to stay home. The increase in e-retail put even more strain on the already strained industry [14].
What is the plan to solve the crisis?
New Fabs
Intel announced in March of 2021 that they were building two new fabrication plants in Arizona, USA, to the tune of $20 billion US dollars [20].
TMSC is also looking to expand into the US, tentatively at first. They are hiring US engineers and executives to do a year’s training in Taiwan before returning to work at the new facilities in Arizona [21].
Samsung will start construction of a new fab in Texas in the first half of 2022. It expects it to be operational in the second half of 2024 [22].
Texas Instruments plans to expand its current operations with 4 new fabs at a cost of $30 billion USD [22].
There are other fabs being built around the world, such as singapore and the EU, as the supply chain has shown its problems.
Most of these new fabs are expected to come online and begin production sometime in 2023 or 2024, and whilst we can be encouraged at the positive impact these will bring to reducing the crisis in the long-term, , there is no short-term relief to the current problem
Predictions from experts
Pat Gelsinger, CEO of Intel - “The global chip shortage is set to last until 2023. Demand continues to soar amid the coronavirus pandemic even as semiconductor manufacturers rush to expand production.”
Lisa Su, CEO of AMD - “The global chip shortage will become less severe in the second half of 2022. We’ve always gone through cycles of ups and downs, where demand has exceeded supply, or vice versa,this time, it’s different.”
Gina Raimondo, Commerce Secretary for the Biden administration - “We aren’t even close to being out of the woods as it relates to the supply problems with semiconductors. There is a significant, persistent mismatch in supply and demand for chips. The semiconductor supply chain remains fragile.”
Conclusion
Problems with the supply of semiconductor chips, both in terms of maxed out production, lean manufacturing and supply chain fragility, were prevalent well before the global pandemic sent demand out-of-control.
A global work-force that is negotiating working-from-home, sickness and self-isolation has all had a significant impact on supply chains and halted many ships, ports and distribution stations. Couple this with severe events such as droughts and fires, and the pressure on the supply end magnifies.
As the Trade-war between China and the US continues, with no new policies on either side to resolve this, the underlying politics of the supply chain problems remain unresolved as well. [23]. The private sector is betting on geographical diversification, such as companies primarily based in East Asia building new fabs in the U.S. or the E.U., or vica versa, as a solution to alleviate the political situation[19].
The chip shortage has certainly presented many challenges for businesses locally and globally, and here at Beta Solutions we are no exception. What has resulted out of this though, are many opportunities to problem solve and explore new ways to do things to alleviate delays in delivery and price increases as a result of this global shortage.
Keep an eye out for part 2 of Global Chip Shortage - New ways of doing things, where we will share some of ways of working with you.
References:
- The Chip Shortage Is Driving Up Tech Prices—Starting With TVs
https://www.wired.com/story/chip-shortage-electronics-prices-tvs-displays/
- Nissan to make half a million fewer cars in 2021 due to chip shortag https://www.cnbc.com/2021/05/13/nissan-to-make-half-a-million-fewer-cars-in-2021-due-to-chip-shortage.html
- Inside the GPU Shortage: Why You Still Can't Buy a Graphics Card https://www.pcmag.com/news/inside-the-gpu-shortage-why-you-still-cant-buy-a-graphics-card
- PBS Why is There a Global Chip Shortage? https://www.youtube.com/watch?v=YEtu9JbDih0
- WSJ Why the Global Chip Shortage Is Hard to Overcome https://www.youtube.com/watch?v=FP_g-as29x0
- List of semiconductor fabrication plants https://en.wikipedia.org/wiki/List_of_semiconductor_fabrication_plants
- Coronavirus pandemic exposes fatal flaws of the 'just-in-time' economy https://www.abc.net.au/news/2020-05-02/coronavirus-pandemic-exposes-just-in-time-economy/12206776
- Secretive Giant TSMC’s $100 Billion Plan To Fix The Chip Shortage https://www.youtube.com/watch?v=GU87SH5e0eI
- Why Taiwan’s drought means you can’t have a new smart TV https://www.smh.com.au/world/asia/why-taiwan-s-drought-means-you-can-t-have-a-new-smart-tv-20210524-p57uq1.html
- Parched Taiwan prays for rain as Sun Moon Lake is hit by drought https://www.theguardian.com/environment/2021/may/09/parched-taiwan-prays-for-rain-as-sun-moon-lake-is-hit-by-drought
- UPDATE 10 - Notice Regarding the Semiconductor Manufacturing Factory (Naka Factory) Fire: Production Capacity Recovery Status https://www.renesas.com/us/en/about/press-room/update-10-notice-regarding-semiconductor-manufacturing-factory-naka-factory-fire-production-capacity
- Fire at vital tech factory could worsen global computer chip shortage https://www.newscientist.com/article/2303316-fire-at-vital-tech-factory-could-worsen-global-computer-chip-shortage/
- Texas winter storm blackouts hit chip production https://www.ft.com/content/ec2f93ad-d23c-4ff4-867a-59385d1cc8a6
- 14 You shopped like never before. The supply chain couldn't handle it https://www.cnet.com/news/features/you-shopped-like-never-before-the-supply-chain-couldnt-handle-it/
- PCB Maker Nittobo Suffers Major Fire That Could Drive Hardware Price Hike https://hardwaresfera.com/en/noticias/hardware/incencio-nittobo-pcb-hardware/
- AKM Factory Fire—A Pro-Audio Industry Disaster
https://www.prosoundnetwork.com/business/akm-factory-fire-shakes-up-pro-audio-industry
- Understanding the global chip shortage, a big crisis involving tiny components https://www.popsci.com/technology/global-chip-shortage/#:~:text=What%20is%20the%20chip%20shortage,rippled%20up%20the%20supply%20chain.
- Why the Chip Shortage Hasn’t Been Fixed Yet https://slate.com/technology/2021/11/chip-shortage-semiconductors-demand-pandemic.html
- The Global Chip Shortage: A Timeline of Unfortunate Events https://info.fusionww.com/blog/the-global-chip-shortage-a-timeline-of-unfortunate-events
- Intel is spending $20 billion to build two new chip plants in Arizona https://www.cnbc.com/2021/03/23/intel-is-spending-20-billion-to-build-two-new-chip-plants-in-arizona.html
- Taiwan’s TSMC begins hiring push for $12 billion Arizona facility https://www.taiwannews.com.tw/en/news/4085851
- Texas To Get Multiple New Fabs as Samsung and TI to Spend $47 Billion on New Facilities https://www.anandtech.com/show/17086/texas-to-get-multiple-new-fabs-as-samsung-and-ti-to-spend-47-billion-on-new- facilities#:~:text=Samsung%20will%20start%20construction%20of,up%20all%20the%20necessary%20equipment.
- The supply-chain disaster that is eating Christmas is being driven by a Biden-Xi conflict that many are overlooking https://www.businessinsider.com.au/supply-shortages-semiconductor-chips-crisis-us-china-trade-war-biden-2021-10?r=US&IR=T